Ciśnienie | do 13 barów, 188 funtów/cal2 |
---|---|
Moc silnika: | do 8 500 kW, 11 500 KM |
Technologia | Sprężarki odśrodkowe wielostopniowe GT |
Wydajność | 33 000 do 100 000 m3/godz., 20 000 do 60 000 stóp3/min |
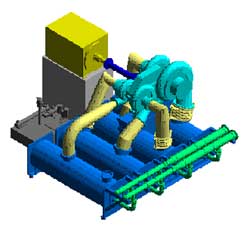
Sprężarki te oferują bardzo duże możliwości sprężarek gazowych serii GT przy konkurencyjnej cenie dzięki standaryzacji.
- Optymalna konstrukcja wirnika i optymalne odcięcia przepływu zapewniające doskonałą efektywność.
- Nastawne łopatki prowadnicy wlotu (IGV) z centralnym stożkiem zapewniające szeroki zakres sterowania i rozruch niskiej mocy.
- Wysokowydajneuszczelnienia z pływającym pierścieniem węglowym, ograniczające dominimum przecieki gazu oraz zapewniające bezstykową pracę,bezpieczeństwo i niezawodność.
- Suche sprzęgło tarczowe z wkładką sprężystą na skręcanie z krótkim odcinkiem wstawianego wału, umożliwiającym łatwy montaż.
- Osiowe łożysko oporowe na wysokoobrotowym małym kole zębatym.
- Wysokoobrotowełożyska poprzeczne/oporowe z podkładkami regulacyjnymi promieniowegołożyska, z wahliwymi płytkami do osiowego centrowania i łożysko oporoweo stożkowej powierzchni styku.
- Zwarta, scalona rama z wbudowanąchłodnicą, dająca wyjątkową sztywność na skręcanie i pozwalająca nałatwy montaż na miejscu dzięki prefabrykacji w warsztacie ACT.
- Znormalizowane moduły sterowania i różne opcje kompletów przyrządów.
- Wspornikdla silnika może znajdować się na wbudowanej chłodnicy gazu (GT063), nabetonowym cokole lub na oddzielnej ramie stalowej (GT078/GT087).
Wbudowana niezawodność
Niezwykle sprawne uszczelnienia firmy Atlas Copco z pływającym pierścieniem węglowym
- Uszczelnienie gazowe minimalizujące przecieki
- Bezstykowe
- Bezpieczne
- Niezawodne
- Referencje i doświadczenie eksploatacyjne z ponad 1000 uszczelnień dla niskich temperatur, wysokich temperatur i agresywnych gazów
Łożyska promieniowe
Koło zębate wysokoobrotowez promieniowym łożyskiem z wahliwymi płytkami.
Łożyska oporowe
Kombinowane łożyska promieniowo-osiowe po stronie niskich obrotów.
Konstrukcja chłodnicy gazu
- Konstrukcja standardowa: woda w rurach, gaz w płaszczu
Wbudowana w ramę fundamentową - Projekt zgodny z AD — Merkblatt lub ASME VIII Div. 2
- Wytwarzane zgodnie z różnymi standardami TEMA
- Elastyczność w doborze materiałów zgodnie z lokalnymi przepisami i kodami: TÜV, Stoomwezen, Codap, Racolta, BS 5500 itd.
Sprzęgło
- Niezwykle elastyczne sprzęgło wielotarczowe
- Nie trzeba konserwować, nie zużywa się
- Elastyczne pod względem skrętnym dzięki wałowi dystansowemu
- Opcja API 671
Elementy sterowania
Sterownik programowalny nadzoruje parametry robocze.
Dostępne w handlu sterowniki programowalne są wykorzystywane do monitorowania i sterowania sprężarkami. Dzięki temu klienci mogą nabyć urządzenia u lokalnego sprzedawcy. Programowanie jest przeprowadzane przez inżynierów firmy Atlas Copco, którzy są ekspertami w dziedzinie zarówno sprężarek, jak i technologii oprogramowania stosowanego do sterowania, dzięki czemu zapewniają optymalną eksploatację.
Te dostosowywalne systemy sterowania ustanawiają nowe standardy w dziedzinie niezawodności i bezpieczeństwa pracy sprężarek dzięki nieustannemu monitorowaniu danych dotyczących temperatury, ciśnienia i drgań oraz automatycznie regulowanym elementom sterowania, zapewniając w ten sposób optymalną pracę i efektywność. Wadliwe działanie sprężarki powoduje automatyczne uruchomienie alarmu lub jej wyłączenie.
W systemach sterowania wprowadzono elementy sterowania dostępne w menu z danymi ciśnienia powietrza na tłoczeniu, temperatury i innych parametrów pracy wyświetlanymi na monitorach CRT lub LCD w wymaganych jednostkach. Wszystkie odnośne ustawienia można zaprogramować stosowanie do określonych wymagań.
Wraz ze zmieniającym się zapotrzebowaniem na sprężone powietrze standardowy system sterowania GT reaguje korektami „pełne obciążenie/bez obciążenia”. Reakcja na zapotrzebowanie powietrza w systemie jest początkowo sterowana przez zawór dławiący lub opcjonalne łopatki kierujące wlotu. Gdy zapotrzebowanie na powietrze spadnie poniżej poziomu wyłączenia sprężarki — stan „bez obciążenia” — sprężarka zostanie całkowicie odciążona. Gdy ciśnienie powietrza w systemie osiągnie najniższy dopuszczalny poziom, sprężarka będzie w pełni obciążona i cykl sterowania zostanie powtórzony.
Opcjonalny system przewidywania niestabilnej pracy
Możliwe jest dostarczenie opcjonalnego systemu przewidywania niestabilnej pracy w celu zapewniania bezpiecznego działania sprężarki po przekroczeniu limitu skoku przy jednoczesnym zachowaniu możliwie największej kontroli nad wyłączeniem w różnych warunkach na wlocie. System nieustannie monitoruje temperatury na wlocie i oblicza ustawienia sterowania wymagane do osiągnięcia najwyższej efektywności pracy sprężarki i zredukowania wydmuchów sprężonego powietrza.
Możliwość zintegrowania sterowania sprężarką z automatyką instalacji użytkownika
Systemy sterowania GT można podłączyć do centralnego systemu sterowania za pośrednictwem połączeń RS232C, RS485 lub innych sieciowych systemów magistrali danych i pętli prądowych w celu zapewnienia efektywnego monitorowania i sterowania. Monitorowanie zdalne można uzyskać za pomocą opcjonalnych wskaźników systemów sterowania i alarmów połączonych ze sterowaniem centralnym za pośrednictwem modemu. System ten ogranicza konieczność nadzoru lokalnego do minimum.
Zastosowania
Doskonała harmonia.
Choć nie największa we Francji ani nie najnowocześniejsza, rafineria Esso w Fos-sur-Mer bez wątpienia wyróżnia się swoją elastycznością produkcji. Elastycznością, która nigdy nie zawiodła przez blisko trzy dziesięciolecia i która właściwie odzwierciedla polityczne i ekonomiczne wrzenie, na które czarne złoto jest tak wrażliwe.
Dodawanie wartości do baryłek ropy
Pierwszy zakład, który później stał się drugim centrum rafinacji we Francji, Esso/Fos, rozpoczął produkcję w 1965 w pobliżu Etang de Berre. Początkowo wydajność produkcji wynosiła 3 miliony ton metrycznych rocznie (t/r) dostarczanych głównie przez zespół destylacji, zespół krakingu katalitycznego, zespół reformowania katalitycznego i układ urządzeń pomocniczych łącznie ze zbiornikami do składowania oraz zespołami uzdatniania wody i odsiarczania.
Od samego początku nie zaniedbano niczego, aby ograniczyć wpływ na środowisko łącznie z ochroną przed zanieczyszczeniami (szczególnie zaawansowanymi od czasu, gdy obrabiano ropę o niskiej zawartości siarki) i zastosowaniem koloru w celu wkomponowania urządzeń w krajobraz śródziemnomorski. Połączona z morskim portem Fos rafineria została uruchomiona i utrzymywała swoje produkcyjne tempo przez osiem lat pod czujnym okiem personelu. Następnie seria wydarzeń przyspieszyła jej ewolucję:
1973 — wojna w święto Jom Kipur. Pierwszym wstrząsem dla rafineria Esso/Fos był okres znacznego wzrostu, gdy produkcja wzrosła z 3 do 8 milionów ton ropy na rok. Oprócz zespołu destylacji atmosferycznej o wydajności 5 milionów ton rocznie zbudowano drugi zespół do reformowania katalitycznego. W tym samym czasie zainstalowano zespoły do odsiarczania i odzyskiwania siarki dla benzyny, nafty i oleju napędowego oraz nowe urządzenie do wytwarzania pary. Powiększono również pojemność magazynową do odbierania ropy surowej i dla gotowych produktów. Całkowita wielkość produkcji sięgnęła 600 000 m3 (3,7 miliona baryłek) i była dostosowana do odpowiednich możliwości transportowych. Połowa była transportowana statkami, a reszta ciężarówkami lub rurociągiem.
1976 — gwałtowny rozwój komputerów przyczynił się również do postępu. Komputery zaczęły coraz bardziej współpracować przy optymalizacji operacji i uzyskiwaniu większej wartości z baryłki ropy, ponieważ podczas rafinowania zasadniczo należy brać pod uwagę trzy czynniki. Zapotrzebowanie, które wyraźnie rośnie i jest wrażliwe na koszty, dostępną ropę i charakterystyki urządzeń klienta.
1980 — ze względów środowiskowych dopuszczalna zawartość siarki w olejach napędowych została ograniczona do maksimum 0,3%. Rafineria Esso/Fos została odpowiednio wyposażona i uzyskała jeszcze większą elastyczność. Rafineria była w stanie przetwarzać różne rodzaje ropy z Bliskiego Wschodu, ze Środkowej Ameryki, ze Związku Radzieckiego, z Afryki itp.
1986 — zdolność produkcyjna spadła do 5 milionów ton rocznie przy wzroście znaczenia optymalizacji i płynności. Aby stać się bardziej konkurencyjną, rafineria ponownie przystosowała swoje urządzenia produkcyjne. Pojemność magazynowa została zwiększona do 1,8 miliona m3 (3,1 miliona acfm), a instalacja produkcyjna osiągnęła zdolność wytwarzania wszystkich rodzajów benzyny na rynki międzynarodowe. Tendencja na następne dziesięciolecie została określona z akcentem zdecydowanie na jakość niż na ilość. Selektywne inwestycje pozwoliły rafinerii odpowiedzieć na wzrastające zapotrzebowanie na paliwa bezołowiowe (stanowiące 35% całkowitej sprzedaży benzyny we Francji w 1992 roku) i na dalsze zmniejszenie zawartości siarki w destylatach.
Sprężone powietrze i kraking katalityczny
Chociaż rafinacja jest głównie destylowaniem, destylacja jest tylko etapem w produkcji benzyny. Destylacja nie tylko nie nadaje się do dostarczania wysokooktanowych paliw wymaganych przez dzisiejsze silniki, ale ilość otrzymywanej w ten sposób benzyny jest również niedostateczna, aby zaspokoić zapotrzebowanie. Dla złagodzenia tych dwóch problemów stosuje się kraking lub reformowanie katalityczne, w zależności od ciężkości destylatów. Ten ważny proces, wymagający sprężonego powietrza, jest właśnie przedmiotem niniejszego artykułu. Kraking jest w zasadzie przemianą cięższych frakcji węglowodorów w benzynę. W tym celu ciężkie molekuły poddaje się działaniu ciepła w obecności katalizatora składającego się z drobnych granulek, które cyrkulują jako ciecz.
Wynaleziony przez Exxon i stosowany dzisiaj przez większość rafinerii proces ten, znany jako kraking fluidyzacyjny, potrzebuje dwóch podstawowych składników — reaktora i regeneratora. Kolejność jest łatwa do zrozumienia. Ciężkie molekuły są krakowane w reaktorze i pozostawiają zawarty w nich węgiel w granulkach katalizatora. Kiedy są już nasycone, usuwa się je do regeneratora, gdzie przywracana jest ich zdolność adsorpcyjna.
Oprócz podgrzewania do temperatury ponad 400°C (750°F) krakowanie fluidyzacyjne wymaga dużych ilości sprężonego powietrza, aby zapewnić dwie funkcje — utrzymanie ciśnienia koniecznego dla procesu i zasilanie spalania potrzebnego do regenerowania katalizatora. Kiedy rafineria Esso w Fos-sur-Mer została uruchomiona w 1965 roku, powietrze do zespołu krakowania było dostarczane przez jednowałową, wielostopniową sprężarkę odśrodkową.
Sprężarka pomocnicza — rozwiązanie zaawansowane technologicznie
Konfiguracja pozostała taka sama aż do roku 1992, kiedy podjęto kroki w celu zwiększenia wydajności krakowania i przepływu sprężonego powietrza. Podjęto zatem decyzję zainstalowania drugiej sprężarki, pracującej równolegle. Problem był delikatny — potrzebna była bardzo specyficzna sprężarka, która nie zakłóciłaby równowagi produkcji rafinerii Fos/Esso. W wyborze przyszłego dostawcy wyposażenia należało zachować największą ostrożność.
„Biorąc pod uwagę charakterystykę głównej maszyny, najlepszy kompromis polegał na dodaniu wysokoobrotowej sprężarki z wbudowaną przekładnią,” podsumowuje Jean David, inżynier urządzeń maszynowych w rafinerii Esso/Fos. Jak wybrano sprężarkę serii GT firmy Atlas Copco? Był to wybór zarówno metodyczny, jak i rygorystyczny.
Skontaktowano się z czołowymi producentami sprężarek i zaproszono ich do przetargu. Firma Atlas Copco dała odpowiedź. „Urządzenie, które zaproponowali, wydawało się interesujące, ale nigdy nie pracowaliśmy z turbosprężarkami firmy Atlas Copco z wbudowaną przekładnią,” mówi Jean David. „Zanim posunęliśmy się dalej, poprosiliśmy o referencje i skonsultowaliśmy się z firmami, które używały już podobnych sprężarek firmy Atlas Copco. Bardzo pozytywne doświadczenie firmy British Petroleum, dotyczące podobnego zastosowania, zachęciło nas do pójścia w tym kierunku. Krok po kroku doszliśmy do wybrania sprężarki modelu GT 050 z wbudowaną przekładnią, zalecanego przez firmę Atlas Copco”.
Zaprojektowana według zaleceń Amerykańskiego Instytutu Naftowego API 672 i przepisów „Podstawowej Praktyki” firmy Esso, sprężarka GT 050 ma następujące parametry: Ciśnienie wlotu 0,945 bara (14 funtów/cal2), ciśnienie tłoczenia 2,785 bara (40 funtów/cal2), pobór mocy 1372 kW (1838 HP) i szybkość przepływu 30 990 m3/h (52 683 acfm) lub 40-50% szybkości przepływu sprężarki głównej. Ze względu na dużą szybkość szczytową i wynikające z niej ograniczenia jej wirnik wykonany jest z tytanu. Aby zapewnić zmienną szybkość przepływu wymaganą przy utrzymywaniu względnie stałego ciśnienia tłoczenia, sprężarka jest wyposażona w system regulacji przepływu posiadający nastawne łopatki dyfuzora.
„Pracując w sieci od 1992 roku potwierdziła całkowicie wyniki z prób odnośnie zarówno charakterystyki termodynamicznej, jak i drganiowej,” dodaje David. W obecnym stanie rzeczy harmonia między dwiema generacjami sprężarek, które nigdy nie były przeznaczone do współpracy ze sobą, okazuje się być doskonała.